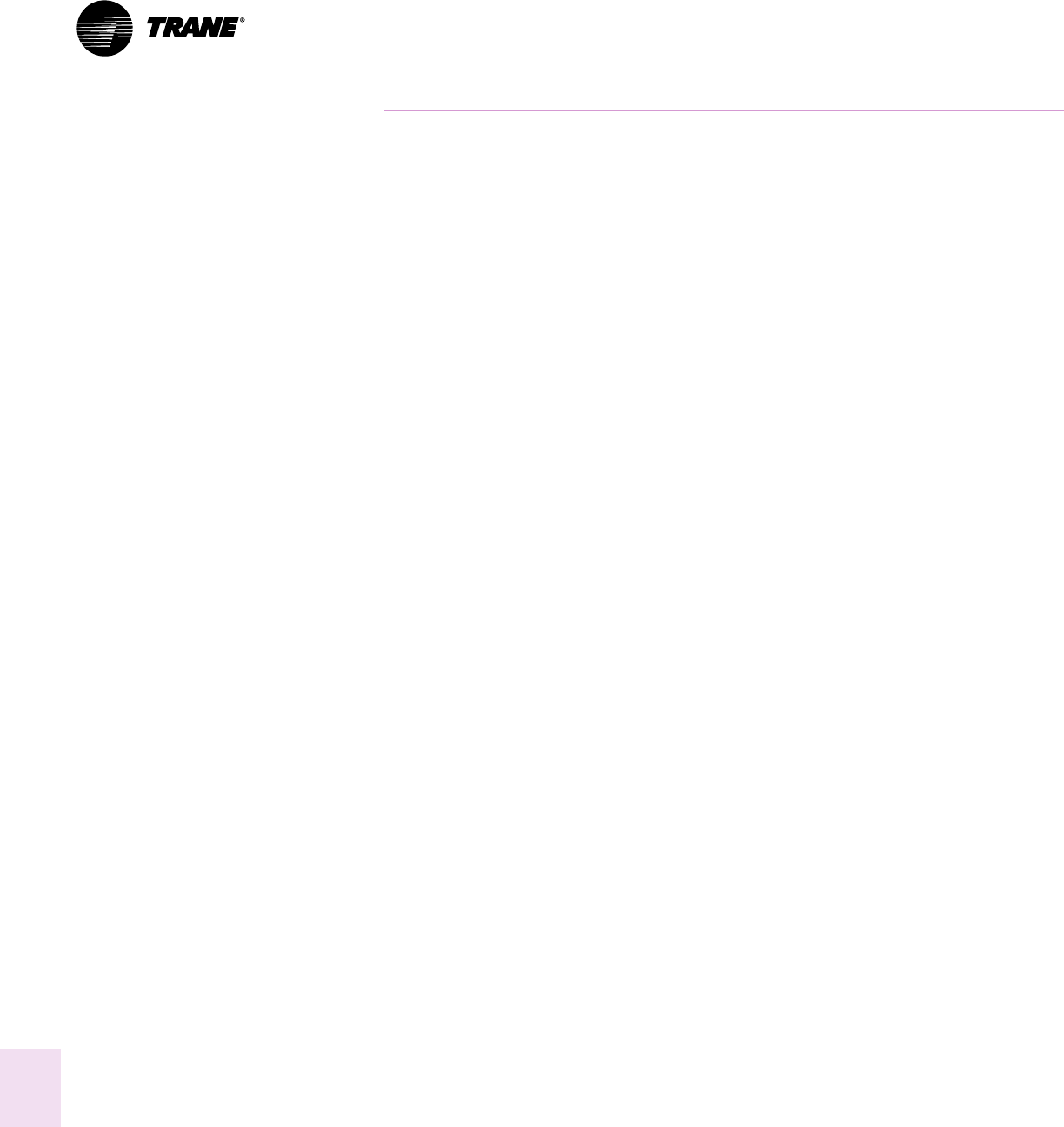
42
MechanicalSpecificationsGeneral
The units shall be dedicated downflow
or horizontal airflow. The operating
range shall be between 115°F and 0°F
(46.1°C and -17.8°C) in cooling as
standard from the factory for all units.
60 HZ cooling performance shall be
rated in accordance with ARI testing
procedures. All units shall be factory
assembled, internally wired, fully
charged with HCFC-22 and
100 percent run tested to check cooling
operation, fan and blower rotation and
control sequence before leaving the
factory. Wiring internal to the unit
shall be numbered for simplified
identification.
Casing
Unit casing shall be constructed of zinc
coated, heavy-gauge, galvanized steel.
All components shall be mounted in a
weather resistant steel cabinet with a
painted exterior. Where top cover
seams exist, they shall be double
hemmed and gasket sealed to prevent
water leakage. Cabinet construction
shall allow for all maintenance on one
side of the unit. Service panels shall
have handles and shall be removable
while providing a water and air tight
seal. Control box access shall be
hinged. The indoor air section shall be
completely insulated with fire resistant,
permanent, odorless glass fiber
material. The base of the unit shall
have provisions for crane lifting.
Filters
Two-inch (51 mm), throwaway filters
shall be standard on all size units.
Two-inch (51 mm) high efficiency,
and four-inch (102 mm) high
efficiency filters shall be optional.
Compressors
All units shall have direct-drive,
hermetic, scroll type compressors with
centrifugal type oil pump providing
positive lubrication to moving parts.
Motor shall be suction gas-cooled and
shall have a voltage utilization range of
plus or minus 10 percent of unit
nameplate voltage. Internal
temperature and current sensitive
motor overloads shall be included for
maximum protection. Shall have
internal sound muffling to minimize
vibration transmission and noise.
External discharge temperature limit,
winding temperature limit and
compressor overload shall be
provided.
Refrigerant Circuits
Each refrigerant circuit shall have
independent thermostatic expansion
devices, service pressure ports and
refrigerant line filter driers factory-
installed as standard. An area shall be
provided for replacement suction line
driers.
Evaporator and Condenser Coils
Condenser coils shall have 3/8 (10 mm)
copper tubes mechanically bonded to
lanced aluminum plate fins. Evaporator
coils shall be 1/2 (13 mm) internally
finned copper tubes mechanically
bonded to high performance
aluminum plate fins. All coils shall be
leak tested at the factory to ensure
pressure integrity. All coils shall be leak
tested to 200 psig and pressure tested
to 450 psig. All evaporator coils shall
be of intermingled configuration.
Outdoor Fans
The outdoor fan shall be direct-drive,
statically and dynamically balanced,
draw through in the vertical discharge
position. The fan motor(s) shall be
permanently lubricated and have built-
in thermal overload protection.
Indoor Fan
Units shall have belt driven, FC,
centrifugal fans with fixed motor
sheaves. All motors shall be circuit
breaker protected.
Electric Heaters
Electric heat shall be available for
factory installation within basic unit.
Electric heater elements shall be
constructed of heavy-duty nickel
chromium elements wye connected for
380 and 415 volt. Staging shall be
achieved through the unitary control
processor (UCP). Each heater package
shall have automatically reset high limit
control operating through heating
element contactors. All heaters shall be
individually fused from factory, where
required, and meet all NEC and CEC
requirements. Power assemblies shall
provide single-point connection.
Gas Heating Section
The heating section shall have a drum
and tube heat exchanger(s) design
using corrosion resistant steel
components. A forced combustion
blower shall supply premixed fuel to a
single burner ignited by a pilotless hot
surface ignition system. In order to
provide reliable operation, a negative
pressure gas valve shall be used that
requires blower operation to initiate
gas flow. On an initial call for heat, the
combustion blower shall purge the
heat exchanger(s) 45 seconds before
ignition. After three unsuccessful
ignition attempts, the entire heating
system shall be locked out until
manually reset at the thermostat. Units
shall be suitable for use with natural
gas or propane (field installed kit). All
units shall have two stage heating.
Controls
Unit shall be completely factory wired
with necessary controls and terminal
block for power wiring. Units shall
provide an external location for
mounting fused disconnect device.
Microprocessor controls shall be
provided for all 24 volt control
functions. The resident control
algorithms shall make all heating,
cooling and/or ventilating decisions in
response to electronic signals from
sensors measuring indoor and outdoor
temperatures. The control algorithm
maintains accurate temperature
control, minimizes drift from set point
and provides better building comfort.
A centralized microprocessor shall
provide anti-short cycle timing and
time delay between compressors to
provide a higher level of machine
protection.
Control Options
Inlet Guide Vanes shall be installed on
each fan inlet to regulate capacity and
limit horsepower at lower system
requirements. When in any position
other than full open they shall pre-spin
intake air in the same direction as fan
rotation. The inlet guide vanes shall
close when supply fan is off, except in
night setback.
The inlet guide vane actuator motor
shall be driven by a modulating dc
signal from the unit microprocessor. A
pressure transducer shall measure duct
static pressure and modulate the inlet
guide vanes to maintain the required
supply air static pressure within a
predetermined range.