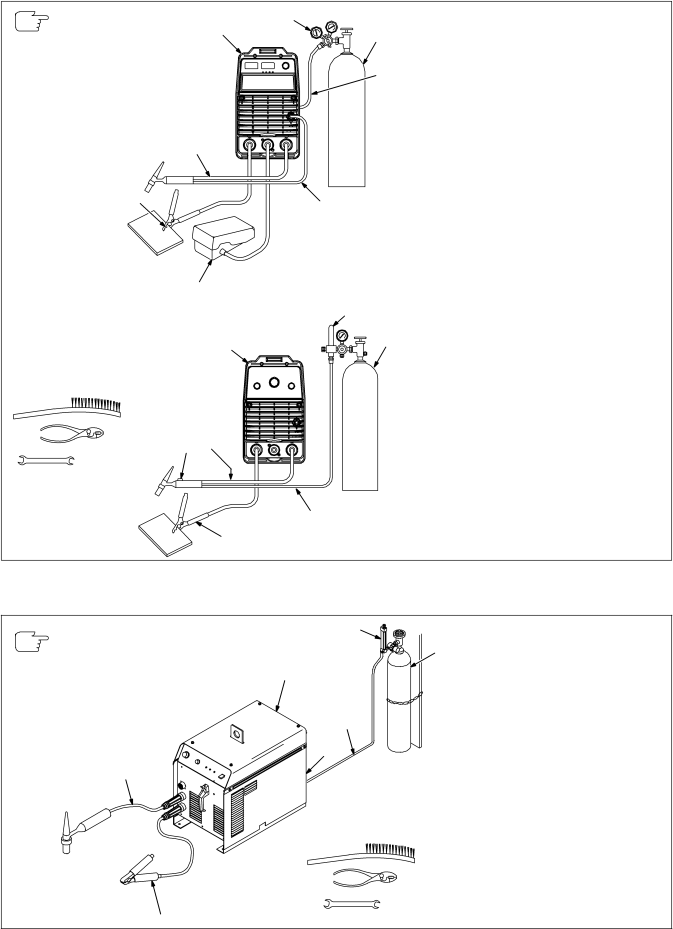
B. Connecting Torch With Two-Piece Cable
If applicable, install | 2 |
| 4 | 3 |
|
| |
Torch Without Gas Valve |
| 1 |
|
|
6
7 | 5 |
|
8 | 803 314 |
|
|
YTurn Off welding power source power before install- ing torch.
Obtain the following hose:
1Gas Hose With
Connections:
2Regulator/Flowmeter
3Gas Cylinder
4Welding Power Source
5Torch
6Torch Power Cable
7Work Clamp
Connect work clamp to a clean,
Use wire brush to clean weld joint area.
8 Foot Control |
Torch With Gas Valve
2
9 Gas Valve |
Valve controls gas preflow and
4 −
Tools Needed:
9 6
5/8, 7/8 in
3
postflow. Open valve on torch just before welding.
Preflow is used to purge the imme- diate weld area of atomsphere.
Postflow is required to cool tung- sten and weld, and to prevent con- tamination of tungsten and weld. Af- ter welding, leave valve open about 1 second for every 10 amperes of weld current. Close valve on torch when postflow is finished.
5
7
803
C. Connecting Torch With Flow-Through Type Connection
If applicable, install | 2 | Y Turn Off welding power | |
| source power before install- | ||
|
| ||
|
| 3 | ing torch. |
| 4 | Obtain the following hose: | |
| 1 Gas Hose With | ||
Torch Without Gas Valve |
| ||
|
| Hand Fittings | |
| 1 | Connections: | |
| 2 | Regulator/Flowmeter | |
|
| ||
| 5 | 3 | Gas Cylinder |
| 4 | Welding Power Source | |
6 |
| ||
| 5 | Gas Valve | |
|
| ||
|
| 6 | |
|
| 7 | Work Clamp |
| Tools Needed: | Connect work clamp to clean, paint- | |
|
| free location on workpiece, close to | |
|
| weld area. |
Use wire brush to clean metal at weld joint area.
Ref.
5/8, 7/8 in
7