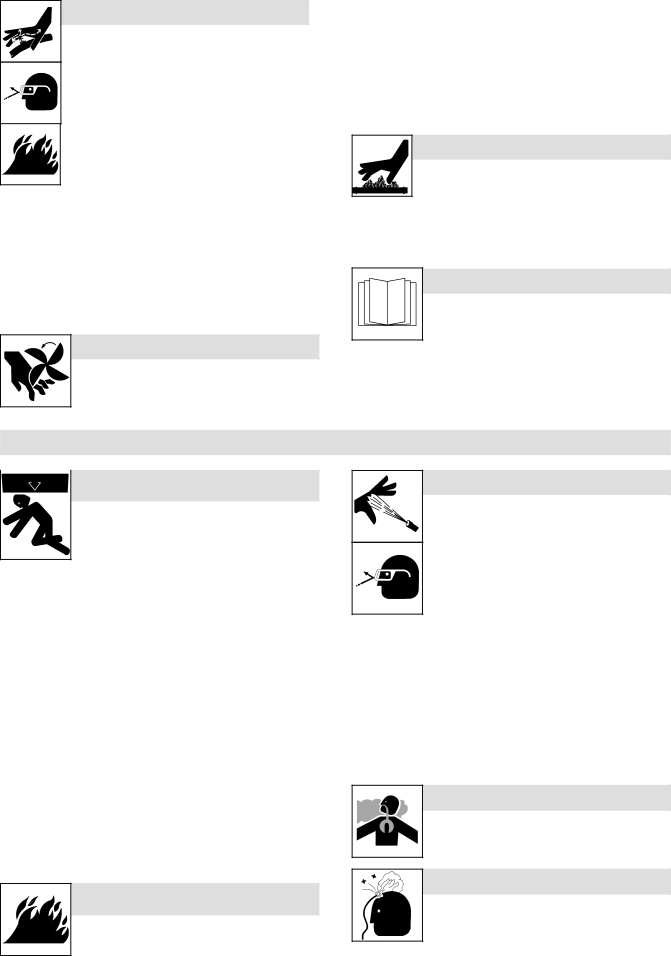
HYDRAULIC FLUID can injure or kill.
D Before working on hydraulic system, turn off and lockout/tagout unit, release pressure, and be sure hydraulic pressure cannot be accidentally applied.
DRelieve pressure before disconnecting or con- necting hydraulic lines.
DCheck hydraulic system components and all con- nections and hoses for damage, leaks, and wear before operating unit.
D Wear protective equipment such as safety glasses, leather gloves, heavy shirt and trousers, high shoes, and a cap when working on hydraulic system.
DUse a piece of paper or cardboard to search for leaks−−never use bare hands. Do not use equipment if leaks are found.
DHYDRAULIC FLUID is FLAMMABLE−−do not work on hydraulics near sparks or flames; do not smoke near hydraulic fluid.
DReinstall doors, panels, covers, or guards when servicing is finished and before starting unit.
DIf ANY fluid is injected into the skin, it must be surgically removed within a few hours by a doctor familiar with this type of injury or gan- grene may result.
MOVING PARTS can injure.
DKeep away from moving parts such as fans,
belts and rotors.
DKeep all doors, panels, covers, and guards closed and securely in place.
DKeep hands, hair, loose clothing, and tools away from moving parts.
DBefore working on hydraulic system, turn off and lockout/tagout unit, release pressure, and be sure hydraulic pressure cannot be accidentally applied.
DHave only qualified people remove guards or covers for maint- enance and troubleshooting as necessary.
DReinstall doors, panels, covers, or guards when servicing is finished and before starting engine.
HOT PARTS AND FLUID can burn.
DDo not touch hot parts bare handed or allow hot fluid to contact skin.
DAllow cooling period before working on equip- ment.
DTo handle hot parts, use proper tools and/or wear heavy, insu- lated welding gloves and clothing to prevent burns.
READ INSTRUCTIONS.
DRead and follow all labels and the Owner’s Manual carefully before installing, operating, or servicing unit. Read the safety information at the beginning of the manual and in each section.
DUse only genuine replacement parts from the manufacturer.
DPerform maintenance and service according to the Owner’s Manuals, industry standards, and national, state, and local codes.
1-5. Compressed Air Hazards
COMPRESSED AIR EQUIPMENT can
injure or kill.
DIncorrect installation or operation of this unit could result in equipment failure and personal injury. Only qualified persons should install, op- erate, and service this unit according to its Owner’s Manual, industry standards, and na- tional, state, and local codes.
DDo not exceed the rated output or capacity of the compressor or any equipment in the compressed air system. Design com- pressed air system so failure of any component will not put people or property at risk.
DBefore working on compressed air system, turn off and lockout/ tagout unit, release pressure, and be sure air pressure cannot be accidentally applied.
DDo not work on compressed air system with unit running unless you are a qualified person and following the manufacturer’s in- structions.
DDo not modify or alter compressor or
DUse only components and accessories approved by the manu- facturer.
DKeep away from potential pinch points or crush points created by equipment connected to the compressed air system.
DDo not work under or around any equipment that is supported only by air pressure. Properly support equipment by mechanical means.
COMPRESSED AIR can injure or kill.
DBefore working on compressed air system,
turn off and lockout/tagout unit, release pres- sure, and be sure air pressure cannot be acci- dentally applied.
DRelieve pressure before disconnecting or con- necting air lines.
DCheck compressed air system components and all connections and hoses for damage, leaks, and wear before operating unit.
DDo not direct air stream toward self or others.
DWear protective equipment such as safety glasses, hearing pro- tection, leather gloves, heavy shirt and trousers, high shoes, and a cap when working on compressed air system.
DUse soapy water or an ultrasonic detector to search for leaks−− never use bare hands. Do not use equipment if leaks are found.
DReinstall doors, panels, covers, or guards when servicing is finished and before starting unit.
DIf ANY air is injected into the skin or body seek medical help im- mediately.
BREATHING COMPRESSED AIR can in- jure or kill.
DDo not use compressed air for breathing.
DUse only for cutting, gouging, and tools.
HOT METAL from air arc cutting and gouging can cause fire or explosion.
DDo not cut or gouge near flammables.
DWatch for fire; keep extinguisher nearby.
TRAPPED AIR PRESSURE AND WHIPPING HOSES can injure.
DRelease air pressure from tools and system be- fore servicing, adding or changing attach- ments, or opening compressor oil drain or oil fill cap.