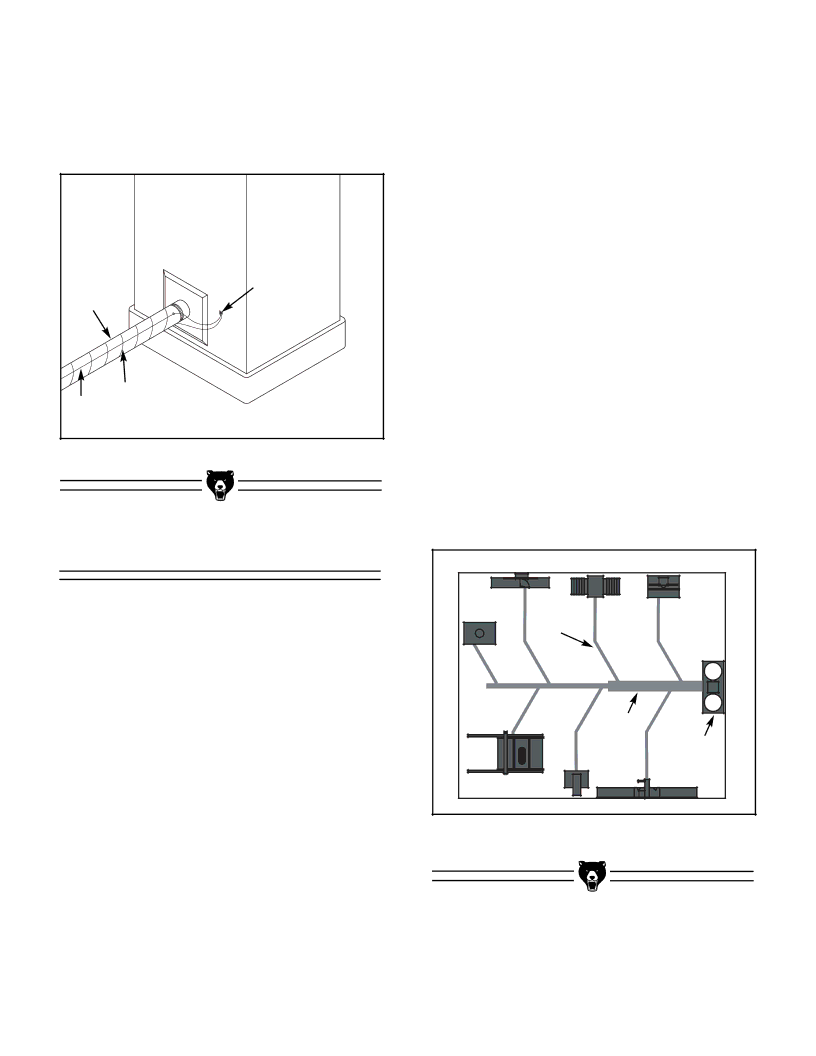
Attach the bare ground wire to each stationary woodworking machine and attach the dust collec- tor frame with a ground screw as shown in Figure
13.Ensure that each machine is continuously grounded to the grounding terminal in your elec- tric service panel.
Ground Screw |
External Ground Wire |
Internal Ground Wire |
Figure 13. Flex-hose grounded to machine.
Design Suggestions
When designing a successful dust collection sys- tem, planning is the most important step. Before you set out to run the first section of duct, consid- er these general guidelines for an efficient sys- tem:
1.Machines that produce the most saw dust should be placed nearest to the dust collector. These machines include thickness planers, shapers, sanders and bandsaws.
2.Ideally you should design the duct system to have the shortest possible mainline run and to have short secondary branch ducts.
3.Directional changes should be kept to a mini- mum. The more directional change fitting you use, the greater the loss of overall static pres- sure.
4.Gradual directional changes are more efficient than sudden directional changes (i.e. use the largest corner radius possible when changing hose or pipe direction).
5.Each individual machine should have a blast gate to control suction from one machine to another.
6.The simpler the system, the more efficient and less costly it will be.
The best way to plan your new system is to draw a bird’s eye view (as shown in Figure 14) of your shop and sketch the following:
1.Your desired location of the dust collector, usually in a corner or along a wall.
2.The location of each machine in the system.
3.The location of the main line duct and each branch line.
4.The location of any obtrusion such as a joist or heating duct, that will require special duct rout- ing.
Branch Line |
Main Line |
Dust |
Collector |
Figure 14. Bird’s eye planning view.
G9958 4 H.P. Dust Collector |