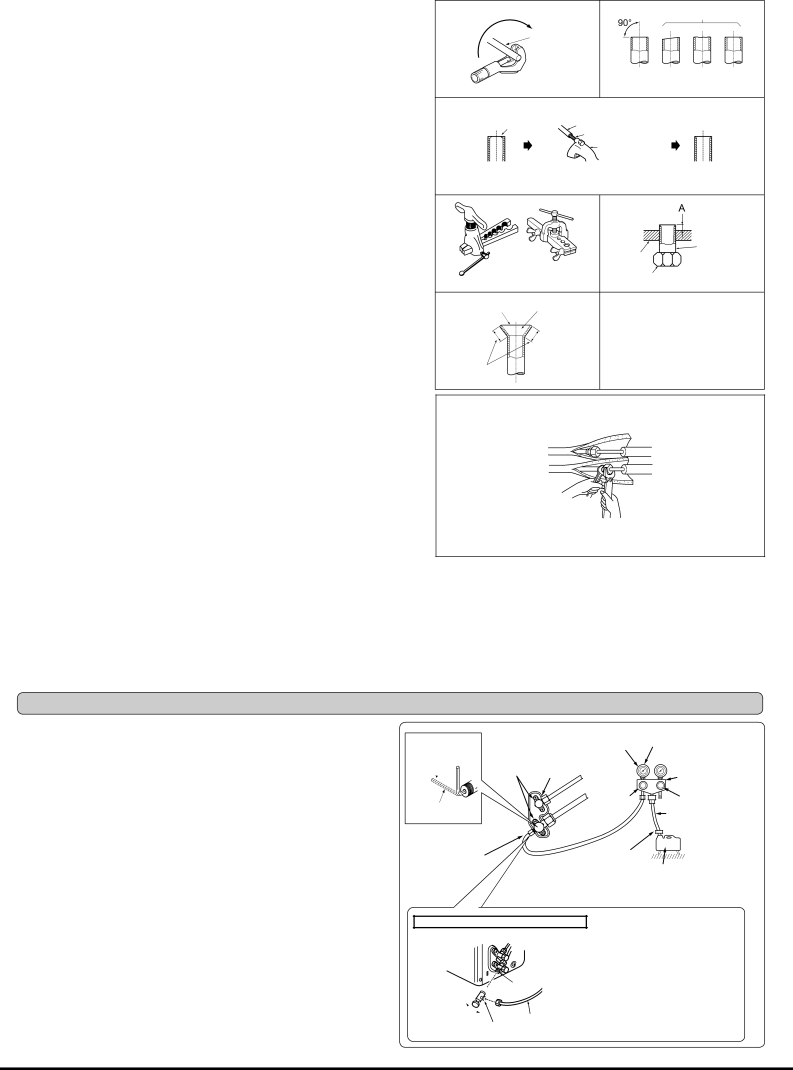
|
| Nut |
| A inch (mm) |
| Tightening torque | ||
Pipe diameter |
|
|
|
|
| |||
inch | Clutch | Clutch | Wing nut |
| ft•lb | |||
inch (mm) |
| |||||||
(mm) | type tool | type tool | type tool | N•m | ||||
|
| (kgf•cm) | ||||||
|
|
| for R410A | for R22 | for R22 |
| ||
|
|
|
|
| ||||
|
|
|
|
|
|
|
| |
ø 1/4 | (6.35) | 1/4 |
|
|
| 13.7 to | 10 to 13 | |
|
| 0.06 to | (140 to | |||||
(17) |
|
| 17.7 | |||||
|
|
|
| 180) | ||||
|
|
|
|
| 0.08 |
| ||
|
|
|
|
|
|
| ||
|
| 3/8 |
|
| (1.5 to | 34.3 to | 25 to 30 | |
ø 3/8 | (9.52) |
|
| 2.0) | ||||
| 0.04 to | (350 to | ||||||
(22) |
|
| 41.2 | |||||
|
| 0 to 0.02 |
| 420) | ||||
|
|
| 0.06 |
|
| |||
|
|
|
|
|
| |||
|
| 1/2 | (0 to 0.5) | (1.0 to |
| 49.0 to | 36 to 42 | |
ø 1/2 | (12.7) |
| 1.5) |
| ||||
| 0.08 to | (500 to | ||||||
(26) |
|
| 56.4 | |||||
|
|
|
| 575) | ||||
|
|
|
|
| 0.10 |
| ||
|
|
|
|
|
|
| ||
|
| 5/8 |
|
| (2.0 to | 73.5 to | 54 to 58 | |
ø 5/8 | (15.88) |
|
| 2.5) | ||||
|
| (750 to | ||||||
(29) |
|
|
| 78.4 | ||||
|
|
|
|
| 800) | |||
|
|
|
|
|
|
| ||
|
|
|
|
|
|
|
|
3-2. FLARE CONNECTION
1)Cut the copper pipe as straight as possible with a pipe cutter. (Fig. 1, 2)
2)Remove all burrs from the cut section of the pipe, ensuring that precautions are taken to avoid getting metal shavings into the piping. (Fig. 3)
5HPRYHÀDUHQXWVDWWDFKHGWRLQGRRUDQGRXWGRRUXQLWVWKHQSXWWKHPRQSLSH
4)Flaring work (Fig. 4, 5). Firmly hold copper pipe in the dimension shown in the table. Select A mm from the table according to the tool you use.
5)Check
&RPSDUHWKHÀDUHGZRUNZLWK)LJ
,IÀDUHLVGHIHFWLYHFXWRIIWKHVHFWLRQDQGUHSHDWSURFHGXUH
|
| Good | No good |
|
| Copper |
|
|
|
| pipe |
|
|
|
|
| Tilted | Uneven | Burred |
| Fig. 1 |
|
| Fig. 2 |
Burr | Copper pipe |
|
| |
| Spare reamer |
|
| |
|
| Pipe cutter |
|
|
|
|
|
| Fig. 3 |
Flaring tool |
|
|
|
|
|
| Die | Copper pipe | |
|
|
|
| |
Clutch type | Wing nut type | Flare nut |
|
|
| Fig. 4 |
| Fig. 5 | |
Smooth all around | Inside is shin- |
|
|
|
ing without any |
|
|
| |
|
|
|
| |
| scratches. |
|
|
|
Even length |
|
|
|
|
all around | Fig. 6 |
|
|
|
3-3. PIPE CONNECTION
)DVWHQÀDUHQXWZLWKDWRUTXHZUHQFKDVVSHFL¿HGLQWKHWDEOHDERYH
:KHQIDVWHQHGWRRWLJKWÀDUHQXWPD\HYHQWXDOO\EUHDNDQGFDXVHUHIULJHUDQWOHDNDJH
Indoor unit connection
Connect both liquid and gas piping to indoor unit.
• Apply a thin coat of refrigerant oil (J) on the seat surface of pipe.
7RFRQQHFW¿UVWDOLJQWKHFHQWHUWKHQWLJKWHQWKH¿UVWWRWXUQVRIÀDUHQXW
• Use tightening torque table above as a guideline for indoor unit side joints, and tighten
XVLQJWZRZUHQFKHV([FHVVLYHWLJKWHQLQJGDPDJHVWKHÀDUHVHFWLRQ
Outdoor unit connection
Connect pipes to stop valve pipe joint of the outdoor unit following the same procedure detailed in Indoor unit connection.
• For tightening, use a torque wrench or spanner.
3-4. INSULATION AND TAPING
1)Cover piping joints with pipe cover.
2)For outdoor unit side, insulate the piping, including valves.
3)Apply piping tape (G) starting from the connection on the outdoor unit.
•When piping has to be installed through a ceiling, closet or where the temperature
DQGKXPLGLW\DUHKLJKXVHDGGLWLRQDO¿HOGVXSSOLHGLQVXODWLRQWRSUHYHQWFRQGHQVD- tion.
4. PURGING PROCEDURES, LEAK TEST, AND TEST RUN
4-1. PURGING PROCEDURES AND LEAK TEST
1) | Remove service port cap of stop valve on the side of the outdoor unit gas pipe. |
2) | Connect gauge manifold valve and vacuum pump to service port of stop valve on the |
| gas pipe side of the outdoor unit. |
3) | Run the vacuum pump 15 minutes or more. |
4) | Check the vacuum with the gauge manifold valve, then close it and shut off the vacuum |
| pump. |
5) | Leave as it is for one or two minutes. Make sure pointer gauge manifold valve remains |
| LQ WKH VDPH SRVLWLRQ &RQ¿UP WKDW SUHVVXUH JDXJH VKRZV ± 03D >*DXJH@ ± |
| LQ+J>±PP+J@ |
6) | Quickly remove gauge manifold valve from service port of stop valve. |
7) | After refrigerant pipes are connected and evacuated, fully open all stop valves on both |
| sides of gas pipe and liquid pipe. Operating the unit without fully opening the valves |
| lowers the performance and causes problems. |
8) | Refer to |
| needed. Be sure to charge slowly with liquid refrigerant. Otherwise, composition of the |
| refrigerant in the system may be changed and affect performance of the air conditioner. |
9) | Tighten cap of service port. |
*4 to 5 turns
*Close
*Open
Hexagonal wrench
Service port cap (Torque 13.7 to
17.7N•m, 140 to
180 kgf•cm)
Stop valve cap (Torque 19.6 to
29.4N•m, 200
WRNJIƒFP
±03D
±LQ+J
>±PP+J@
Stop valve for LIQUID
Handle
Low
Stop valve for
GAS
Adapter for pre- venting the back
ÀRZ
Compound pressure gauge (for R410A)
Pressure gauge (for R410A)
Gauge manifold valve (for R410A)
Handle High
Charge hose (for R410A)
Vacuum pump (or the vacuum pump with the function to SUHYHQWWKHEDFNÀRZ
10) Conduct a leak test |
Precautions when using the control valve
Service port
A
Control valve
Open
Close | Charge hose |
Body
When attaching the control valve to the service port, valve core may deform or loosen if excess pressure is applied. This may cause gas leak.
When attaching the control valve to the service port, make sure that the valve core is in closed position, and then tighten part A. Do not tighten part A or turn the body when valve core is in open position.