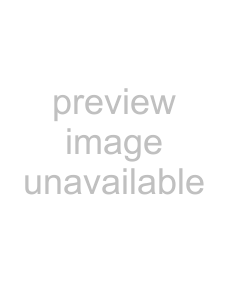
SERIES 28A BOILER INSTALLATION AND OPERATION INSTRUCTIONS | Page 21 |
Install 3" nipples and ball valves in the two 3" NPT front section tappings so the boiler can be blown down.
The feed water requirements for steam boilers at full input are shown in Table 9. The addition of water to the boiler should be controlled by sensing the actual boiler water level. 1" NPT water column tappings are provided on the front section for the mounting of the required water level controls, see Figure 17.
CAUTION: Makeup water connections must be made to the return piping and not to the boiler or the boiler may be damaged voiding the warranty!
Cleaning of Steam Boilers
The burner must be installed and made operational along with the operating, limit and other safety controls. The burner on oil boilers must be adjusted to prevent sooting of the boiler flues. Final burner adjustment should be made after the boiler has been properly cleaned.
CAUTION: Failure to properly clean the boiler can result in foaming and surging and prevent proper operation of the boiler! Boiler damage can occur voiding the warranty!
NOTE: Do not connect the boiler to the return piping until the system piping has been thoroughly flushed or recontamination of the boiler can occur.
1.Plug the 4" NPT return tappings in the back section and any other unused tappings, see step 5 below.
WARNING: The safety valve must be installed and piped to the floor to prevent scalding in the event of a discharge, see Figure 15. The discharge piping must be sized the same as the safety valve outlet. Never install any type of valve between the boiler and the safety valve! Failure to comply with this warning can result in an explosion causing extensive property damage, severe personal injury or death!
2.Fill the boiler with water to a level 1 in., 25.4 mm below the normal water level line of 50 1/2 in., 1.28 m from the floor.
3.Pipe a skimmer off the 6" NPT tapping in the front section using 1 1/2" NPT pipe.
4.Make a cleaning solution by mixing 1 lb, 0.45 kg each off caustic soda and trisodium phosphate for every 50 ga, 189 L of water, see Table 7.
CAUTION: Avoid skin contact with cleaning solution
to prevent injury! If eye or skin contact occurs flush with large quantities of water.
NOTE: Some locations do not allow this solution to be used. Check with the local authority having jurisdiction.
5.Mix the cleaning chemicals with water to create a concentrated solution. Pour the cleaning solution through one of the top tappings in the front section and plug it.
6.Immediately fire the boiler and maintain a steam pressure of 0 to 2 psig, 0 to 13.8 kPa. It may be necessary to cycle the boiler.
WARNING: Monitor the boiler pressure constantly during the cleaning procedure. Do not allow the boiler pressure to exceed 15 PSI, 103 kPa or a discharge of hot water and steam will occur!
7.Adjust the water feed to prevent the build up of pressure within the boiler. Continue the skimming process until the discharge runs clear.
8.Shut the boiler off and allow the boiler to cool to 100° F, 34° C. Remove the skim piping and plug the tapping. Open the blowdown valve and flush the boiler until the discharge runs clear.
9.Close the blowdown valve and fill the boiler with water to a level 1in., 25 mm below the normal water level line.
10.Check the traps and vents for proper operation.
BURNER INSTALLATION
WARNING: The burner must be installed in accordance with the burner manufactures instructions. Check the boiler rating plate to make sure that the boiler is for the type of fuel that will be used. If it isn’t, do not connect the burner to the fuel supply. Failure to comply with this warning can result in extensive property damage, severe personal injury or death!
Follow the burner manufacturer’s installation instructions for the proper installation, fuel piping, wiring, burner adjustment and servicing. Mount the burner per the instructions on page 13.
When applicable, provisions for vent, bleed and gas relief lines must be made in accordance with the latest revision of ANSI Z223.1/NFPA 54.