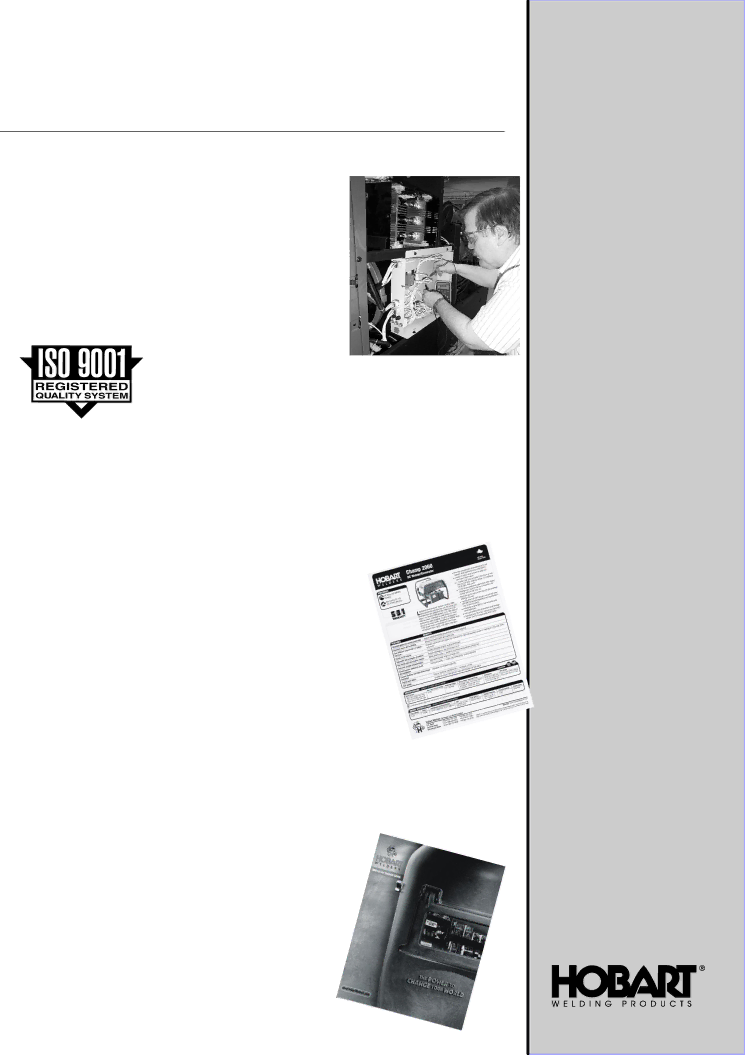
From Hobart to You
Thank you and congratulations on choosing Hobart.
Now you can get the job done and get it done right.
We know you don’t have time to do it any other way.
This Owner’s Manual is designed to help you get the most out of your Hobart products. Please take time to read the Safety precautions. They will help you
|
| protect yourself against |
|
| potential hazards on the |
|
| worksite. We’ve made |
|
| installation and operation |
|
| quick and easy. With Hobart you can count on |
|
| years of reliable service with proper |
|
| maintenance. And if for some reason the unit |
Hobart is | registered to the | needs repair, there’s a Troubleshooting section |
ISO 9001 | Quality System | that will help you figure out what the problem |
Standard. |
| |
| is. The parts list will then help you to decide | |
|
| |
|
| which exact part you may need to fix the |
|
| problem. Warranty and service information for |
|
| your particular model are also provided. |
Hobart Welders manufactures a full line of welders and welding related equipment. For information on other quality Hobart products, contact your local Hobart distributor to receive the latest full line catalog or individual catalog sheets. To locate your nearest
distributor or service agency call 1-877-Hobart1.
Hobart offers a Technical Manual which provides more detailed service and parts information for your unit. To obtain a Technical Manual, contact your local distributor. Your distributor can also supply you with Welding Process Manuals such as SMAW, GTAW, GMAW, and