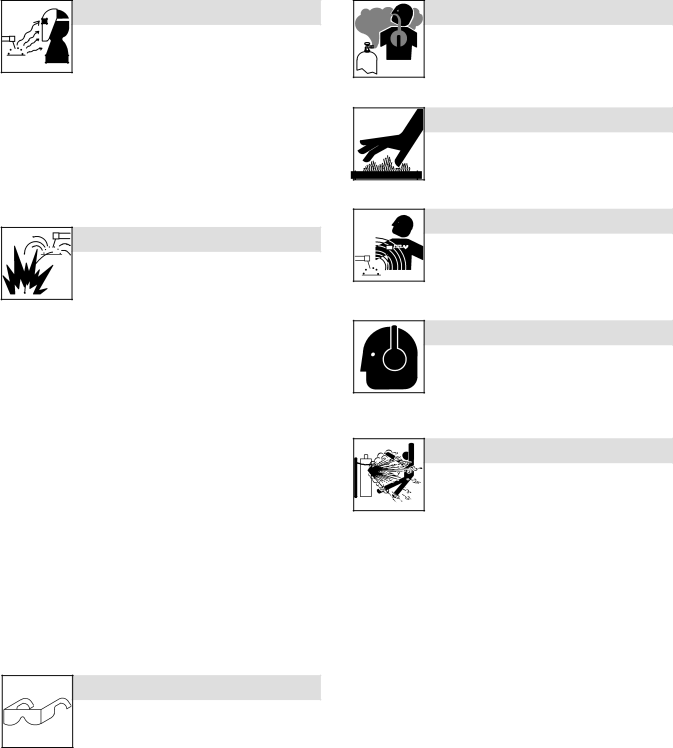
ARC RAYS can burn eyes and skin.
Arc rays from the welding process produce intense visible and invisible (ultraviolet and infrared) rays that can burn eyes and skin. Sparks fly off from the weld.
DWear a welding helmet fitted with a proper shade of filter to protect your face and eyes when welding or watching (see ANSI Z49.1 and Z87.1 listed in Safety Standards).
DWear approved safety glasses with side shields under your helmet.
DUse protective screens or barriers to protect others from flash and glare; warn others not to watch the arc.
DWear protective clothing made from durable,
WELDING can cause fire or explosion.
Welding on closed containers, such as tanks, drums, or pipes, can cause them to blow up. Sparks can fly off from the welding arc. The flying sparks, hot workpiece, and hot equipment can cause fires and
burns. Accidental contact of electrode to metal objects can cause sparks, explosion, overheating, or fire. Check and be sure the area is safe before doing any welding.
DProtect yourself and others from flying sparks and hot metal.
DDo not weld where flying sparks can strike flammable material.
DRemove all flammables within 35 ft (10.7 m) of the welding arc. If this is not possible, tightly cover them with approved covers.
DBe alert that welding sparks and hot materials from welding can easily go through small cracks and openings to adjacent areas.
DWatch for fire, and keep a fire extinguisher nearby.
DBe aware that welding on a ceiling, floor, bulkhead, or partition can cause fire on the hidden side.
DDo not weld on closed containers such as tanks, drums, or pipes, unless they are properly prepared according to AWS F4.1 (see Safety Standards).
DConnect work cable to the work as close to the welding area as practical to prevent welding current from traveling long, possibly unknown paths and causing electric shock and fire hazards.
DDo not use welder to thaw frozen pipes.
DRemove stick electrode from holder or cut off welding wire at contact tip when not in use.
DWear
DRemove any combustibles, such as a butane lighter or matches, from your person before doing any welding.
FLYING METAL can injure eyes.
DWelding, chipping, wire brushing, and grinding cause sparks and flying metal. As welds cool, they can throw off slag.
DWear approved safety glasses with side shields even under your welding helmet.
BUILDUP OF GAS can injure or kill.
D Shut off shielding gas supply when not in use.
D Always ventilate confined spaces or use approved
HOT PARTS can cause severe burns.
DDo not touch hot parts bare handed.
DAllow cooling period before working on gun or
torch.
MAGNETIC FIELDS can affect pacemakers.
D Pacemaker wearers keep away.
D Wearers should consult their doctor before going near arc welding, gouging, or spot welding operations.
NOISE can damage hearing.
Noise from some processes or equipment can damage hearing.
DWear approved ear protection if noise level is high.
CYLINDERS can explode if damaged.
Shielding gas cylinders contain gas under high pressure. If damaged, a cylinder can explode. Since gas cylinders are normally part of the welding process, be sure to treat them carefully.
DProtect compressed gas cylinders from excessive heat, mechani- cal shocks, slag, open flames, sparks, and arcs.
DInstall cylinders in an upright position by securing to a stationary support or cylinder rack to prevent falling or tipping.
DKeep cylinders away from any welding or other electrical circuits.
DNever drape a welding torch over a gas cylinder.
DNever allow a welding electrode to touch any cylinder.
DNever weld on a pressurized cylinder – explosion will result.
DUse only correct shielding gas cylinders, regulators, hoses, and fit- tings designed for the specific application; maintain them and associated parts in good condition.
DTurn face away from valve outlet when opening cylinder valve.
DKeep protective cap in place over valve except when cylinder is in use or connected for use.
DRead and follow instructions on compressed gas cylinders, associated equipment, and CGA publication