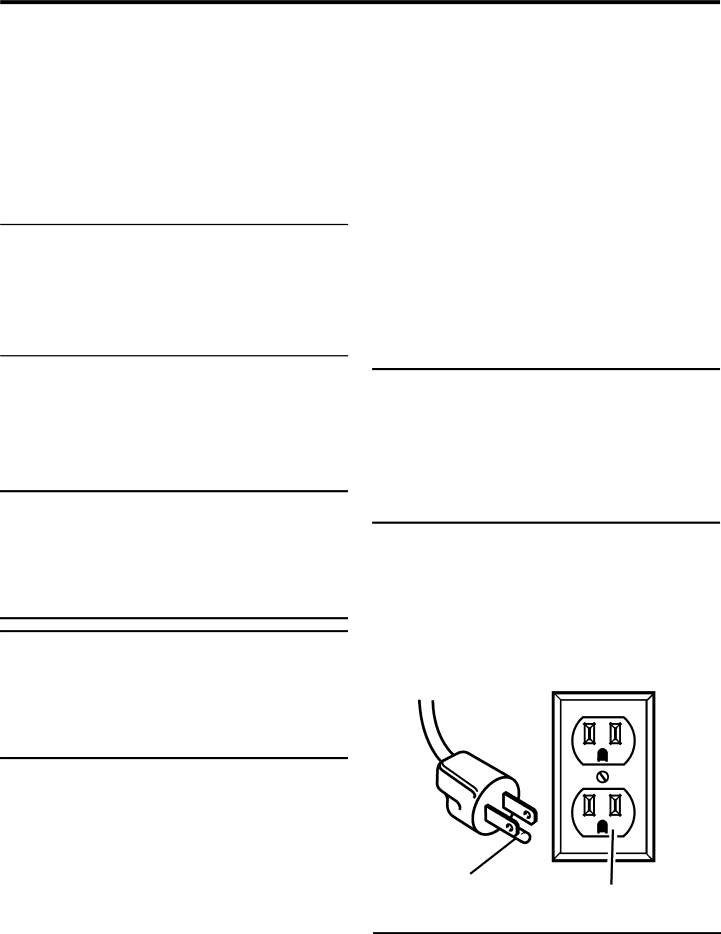
ELECTRICAL
EXTENSION CORDS
Use only
**Ampere rating (on tool faceplate)
| ||||||
|
|
|
| |||
Cord Length | Wire Size (A.W.G.) |
|
| |||
|
|
|
|
|
|
|
25' | 16 | 16 | 16 | 16 | 14 | 14 |
|
|
|
|
|
|
|
50' | 16 | 16 | 16 | 14 | 14 | 12 |
|
|
|
|
|
|
|
100' | 16 | 16 | 14 | 12 | 10 | — |
**Used on 12 gauge - 20 amp circuit. NOTE: AWG = American Wire Gauge
When working with the tool outdoors, use an extension cord that is designed for outside use. This is indicated by the letters “WA” on the cord’s jacket.
Before using an extension cord, inspect it for loose or exposed wires and cut or worn insulation.
WARNING:
Keep the extension cord clear of the working area. Position the cord so that it will not get caught on lumber, tools or other obstructions while you are working with a power tool. Failure to do so can result in serious personal injury.
WARNING:
Check extension cords before each use. If dam- aged replace immediately. Never use product with a damaged cord since touching the damaged area could cause electrical shock resulting in serious injury.
ELECTRICAL CONNECTION
This product is powered by a precision built electric motor. It should be connected to a power supply that is 120 V, 60 Hz, AC only (normal household current). Do not operate this product on direct current (DC). A substantial voltage drop will cause a loss of power and the motor will overheat. If the saw does not operate when plugged into an outlet, double check the power supply.
SPEED AND WIRING
The
GROUNDING INSTRUCTIONS
This product must be grounded. In the event of a malfunction orbreakdown,groundingprovidesapathofleastresistancefor electric current to reduce the risk of electric shock. This tool is
Do not modify the plug provided. If it will not fit the outlet, have the proper outlet installed by a qualified electrician.
WARNING:
Improper installation of the grounding plug is able to result in a risk of electric shock. When repair or replacement of the cord is required, do not connect the grounding wire to either flat blade terminal. The wire with insulation having an outer surface that is green with or without yellow stripes is the grounding wire.
Check with a qualified electrician or service personnel if the grounding instructions are not completely understood, or if in doubt as to whether the tool is properly grounded.
Repair or replace a damaged or worn cord immediately.
This product is for use on a nominal 120 volt circuit and has a grounding plug similar to the plug illustrated in fig- ure 1. Only connect the product to an outlet having the same configuration as the plug. Do not use an adapter with this product.
GROUNDING | 120 V GROUNDED OUTLET |
PIN | |
| Fig. 1 |
8