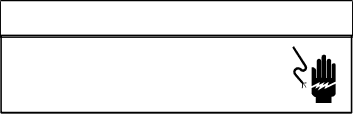
PRIMARY LIMIT
The primary limit control is located on the partition panel and monitors heat exchanger compartment temperatures. It is a
AUXILIARY LIMIT
The auxiliary limit control(s) are located on or near the circulator blower and monitors heat exchanger compartment temperatures. They are a
ROLLOUT LIMIT
The rollout limit control(s) are mounted on the burner/manifold assembly and monitor the burner flame. They are
PRESSURE SWITCHES
The pressure switches are
FLAME SENSOR
The flame sensor is a probe mounted to the burner/manifold assem- bly which uses the principle of flame rectification to determine the pres- ence or absence of flame.
XVIII. TROUBLESHOOTING
ELECTROSTATIC DISCHARGE (ESD) PRECAUTIONS
NOTE: Discharge body’s static electricity before touching unit. An electrostatic discharge can adversely affect electrical components.
Use the following precautions during furnace installation and ser- vicing to protect the integrated control module from damage. By putting the furnace, the control, and the person at the same electro- static potential, these steps will help avoid exposing the integrated control module to electrostatic discharge. This procedure is appli- cable to both installed and uninstalled (ungrounded) furnaces.
1.Disconnect all power to the furnace. Do not touch the integrated control module or any wire connected to the control prior to discharging your body’s electrostatic charge to ground.
2.Firmly touch a clean, unpainted, metal surface of the furnaces near the control. Any tools held in a person’s hand during grounding will be discharged.
3.Service integrated control module or connecting wiring following the discharge process in step 2. Use caution not to recharge your body with static electricity; (i.e., do not move or shuffle your feet, do not touch ungrounded objects, etc.). If you come in contact with an ungrounded object, repeat step 2 before touching control or wires.
4.Discharge your body to ground before removing a new control from its container. Follow steps 1 through 3 if installing the control on a furnace. Return any old or new controls to their containers before touching any ungrounded object.
DIAGNOSTIC CHART
WARNING
HIGH VOLTAGE!
TO AVOID PERSONAL INJURY OR DEATH DUE TO ELECTRICAL SHOCK, DISCONNECT ELECTRICAL POWER BEFORE PERFORMAING ANY SERVICE OR MAINTENANCE.
Refer to the Troubleshooting Chart at the end of this manual for assis- tance in determining the source of unit operational problems. The red diagnostic LED blinks to assist in troubleshooting the unit. The num- ber of blinks refers to a specific fault code.
FAULT RECALL
The ignition control is equipped with a momentary pushbutton switch that can be used to display on the diagnostic LED the last five faults detected by the control. The control must be in Standby Mode (no ther- mostat inputs) to use the feature. Depress the pushbutton switch for approximately 2 seconds. Release the switch when the LED is turned off. The diagnostic LED will then display the flash codes associated with the last five detected faults. The order of display is the most re- cent fault to the least recent fault.
RESETTING FROM LOCKOUT
Furnace lockout results when a furnace is unable to achieve ignition after three attempts during a single call for heat. It is characterized by a
1.Automatic reset. The integrated control module will automatically reset itself and attempt to resume normal operations following a one hour lockout period.
2.Manual power interruption. Interrupt 115 volt power to the furnace for 1 - 20 seconds.
3.Manual thermostat cycle. Lower the thermostat so that there is no longer a call for heat then reset to previous setting. Interrupt thermostat signal to the furnace for 1 - 20 seconds.
NOTE: If the condition which originally caused the lockout still exists, the control will return to lockout. Refer to Troubleshooting - Diagnostic Chart for aid in determining the cause.
39