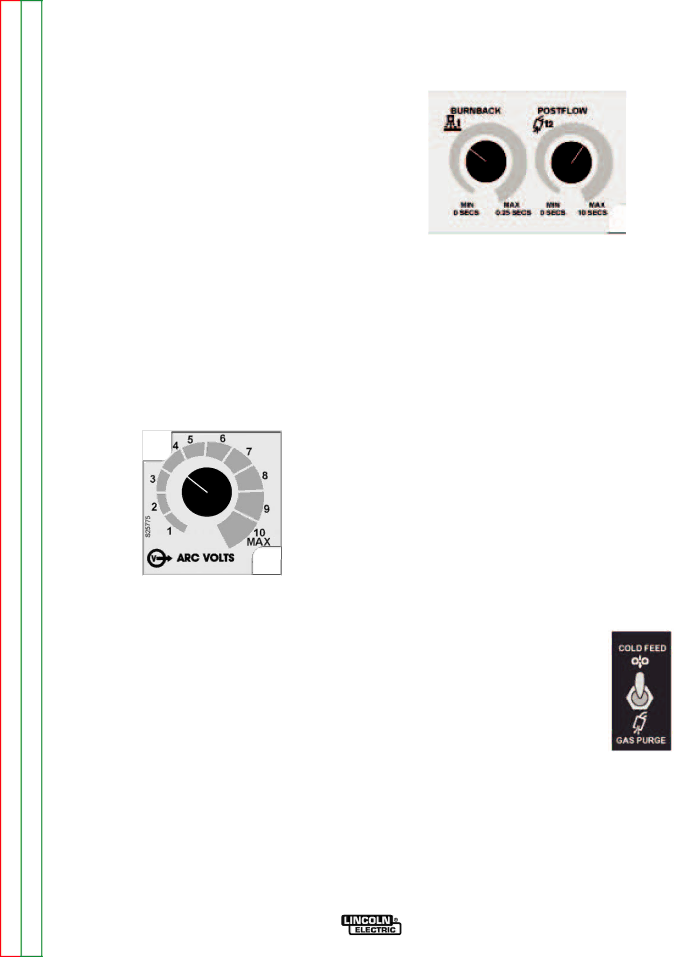
| OPERATION | |
|
|
|
Return to Master TOC
TOC
1. WIRE FEED SPEED KNOB
The large, calibrated wire feed speed knob makes for easy and accurate adjustment of the wire feed speed. The knob rotates 3/4 turn. Turn the knob clockwise to increase the wire feed speed, and counter clockwise to reduce the wire feed speed.
K2426-1 and K2426-2 models:
These wire feeders are factory configured for normal speed operation.
The normal wire feed speed range is 100 to 800 in/min (2.5 - 20.3 m/min).
K2426-3 model:
The wire feed speed range on the extra torque model is 50 to 400 in/min (1.3 – 10.2 m/min)
To set the burnback time, adjust the knob to approxi- mately 0.03 seconds and then decrease or increase the time as desired.
Postflow Timer
The postflow timer range is OFF to 10 seconds. Postflow is the time from when the power source out- put turns OFF until the postflow timer expires. Use postflow to protect the weld while the weld cools.
Return to Section TOC
Return to Section TOC
Return to Section TOC
Return to Section TOC
Return to Master
Return to Master TOC
Return to Master TOC
2. REMOTE VOLTAGE CONTROL KIT
The optional remote voltage control kit adjusts the arc voltage from the minimum to the maximum voltage of the welding power source. Rotate the knob counter- clockwise to reduce the arc voltage and rotate the knob clockwise to raise the arc voltage.
3. BURNBACK AND POSTFLOW TIMER KIT
The optional Burnback and Postflow Timer Kit gives control over the shielding gas at the end of the weld and prepares the end of the wire for the next arc start. Additional shielding gas protection is often required when welding aluminum, stainless steel or exotic alloys.
When stitch welding, set the postflow time to maxi- mum for best results.
Burnback Timer
The burnback timer range is OFF to 0.25 seconds. The burnback timer controls the additional amount of time the power source output remains ON after the wire drive has stopped feeding wire. Burnback adjust- ment prevents the wire from sticking to the weld at the end of a weld and helps to condition the wire for the next weld.
4. THERMAL LED, MOTOR OVERLOAD
The thermal light illuminates when the wire drive motor draws too much current. If the thermal light illu- minates, the wire drive will automatically shutdown for up to 30 seconds to allow the motor to cool. To start welding again, release the gun trigger, inspect the gun cable, liner (and conduit). Clean and make repairs as necessary. Start welding again when the problem has been safely resolved.
For best results, keep the gun cable and conduit as straight as possible. Perform regular maintenance and cleaning on the gun liner, conduit and gun. Always use quality electrode, such as
5. COLD FEED/GAS PURGE SWITCH
Cold Feed and Gas Purge are combined into a single spring centered toggle switch.
To activate Cold Feeding, hold the switch in the UP position. The wire drive will feed electrode but neither the power source nor the gas solenoid will be energized. Adjust the speed of cold feeding by rotat- ing the WFS knob. Cold feeding, or "cold inching" the electrode is useful for thread- ing the electrode through the gun.
Hold the toggle switch in the DOWN posi-
tion to activate Gas Purge and let the shielding gas flow. The gas solenoid valve will energize but neither the power source output nor the drive motor will be turned on. The Gas Purge switch is useful for setting the proper flow rate of shielding gas. Flow meters should always be adjusted while the shielding gas is flowing.