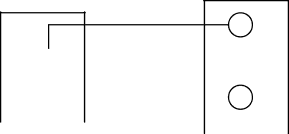
NOTE: Zero input corresponds to zero screw speed and no additive dosing. Maximum input corresponds to maximum screw speed.
NOTE: If a
_ |
|
| + |
|
|
|
| ||
|
|
|
|
|
|
|
|
|
|
|
|
|
|
|
|
|
|
|
|
|
|
|
| |||
|
|
|
|
|
| |||
Extruder output | Digital Dosing controller |
(diagram of frequency inputs)
Figure 6. Frequency Inputs
5.Make sure the unit is turned OFF before plugging it in. The switch toward the rear of the controller unit should be in the OFF, or “O” position. Standard operation voltage is 110 or 220 VAC, 50/60 Hz,
3.2Initial Operation
The control system is
Prior to putting your new Digital Dosing Additive Feeder
•You must enter a recipe and calibrate the feeder.
Digital Dosing Units | 13 |