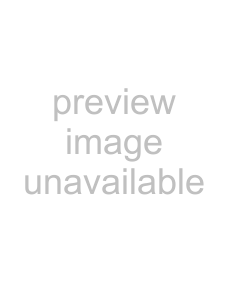
Manual Tuning
In some applications, the autotune process may not provide PID parameters for the process characteristics you desire. If that is the case, you may want to tune the controller manually.
1.Apply power to the controller and establish a set point typically used in your process.
2.Go to the Operations Page, Loop Menu, and set Heat Proportional Band [`h;Pb] and/or Cool Pro- portional Band [`C;Pb] to 5. Set Time Integral [``ti] to 0. Set Time Derivative [``td] to 0.
3.When the system stabilizes, watch the process value. If it fluctuates, increase the Heat Propor- tional Band or Cool Proportional Band value in 3 to 5° increments until it stabilizes, allowing time for the system to settle between adjustments.
4.When the process has stabilized, watch Heat Power [`h;Pr] or Cool Power [`C;Pr] (Operations Page, Monitor Menu). It should be stable ±2%. At this point, the process temperature should also be stable, but it will have stabilized before reach- ing the set point. The difference between the set point and actual process value can be eliminated with Integral.
5.Start with an Integral value of 6,000 and allow 10 minutes for the process temperature to reach the set point. If it has not, reduce the setting by half and wait another 10 minutes. Continue re- ducing the setting by half every 10 minutes until the process value equals the set point. If the pro- cess becomes unstable, the Integral value is too small. Increase the value until the process stabi- lizes.
6.Increase Derivative to 0.1. Then increase the set point by 11° to 17°C. Monitor the system’s ap- proach to the set point. If the process value over- shoots the set point, increase Derivative to 0.2. Increase the set point by 11° to 17°C and watch the approach to the new set point. If you increase Derivative too much, the approach to the set point will be very sluggish. Repeat as necessary until the system rises to the new set point with- out overshoot or sluggishness.
For additional information about autotune and PID control, see related features in this chapter.
Autotuning with TRU-TUNE+®
The
The preferred and quickest method for tuning a loop is to establish initial control settings and continue with the adaptive mode to fine tune the settings.
Setting a controller's control mode to tune starts this
Once the process variable has been at set point for a suitable period (about 30 minutes for a fast process to roughly two hours for a slower process) and if no further tuning of the PID parameters is desired or needed,
Once the PID parameters have been set by the
Turn
Use
Use
Before Tuning
Before autotuning, the controller hardware must be installed correctly, and these basic configuration parameters must be set:
•Sensor Type [`SEn] (Setup Page, Analog Input Menu), and scaling, if required;
•Function [``Fn] (Setup Page, Output Menu) and scaling, if required.
How to Autotune a Loop
1.Enter the desired set point or one that is in the middle of the expected range of set points that you want to tune for.
2.Enable
Watlow | • 55 • | Chapter 9 Features |