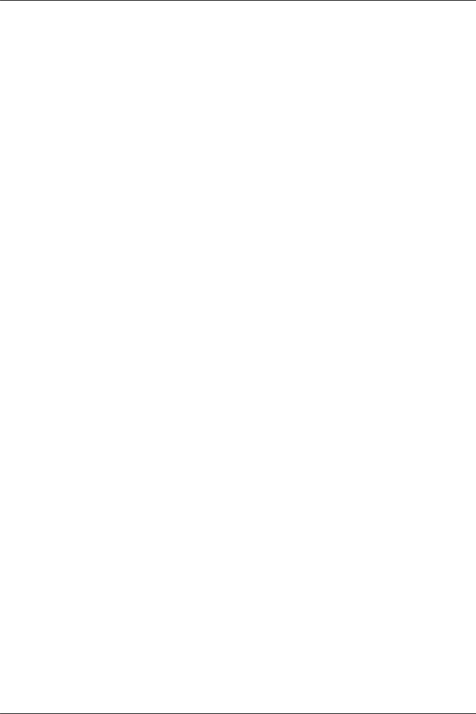
www.supportme.net
B.1.1 Servo configuration
The servo configuration is the default configuration for the drive, allowing the motor control system to operate as a torque controller, a velocity controller or a position controller. This configuration comprises 3 nested control loops; a current control loop, a velocity control loop and a position control loop, as shown in Figure 51.
The universal encoder interface reads rotor position from the encoder and estimates velocity. The commutation block uses the position to calculate the electrical angle of the rotor. The current sensor system measures U and V phase currents. These are fed into a current conversion block that converts them into quantities representing torque producing and magnetizing currents (the ’vector’ currents which are locked to the rotor).
In the current control loop, a current demand and the final measured current values form the inputs to a PI (Proportional, Integral) control system. This control system generates a set of voltage demands that are fed into a PWM
The torque controller converts a torque demand into a current demand and compensates for various load
In the velocity control loop, a velocity demand and measured velocity form the inputs to a PI control system. The output of the control system is a torque demand which, when the drive is operating as a velocity controller, forms the input to the current control loop.
Finally, in the position control loop, a position demand and measured position form the inputs to a PID (Proportional, Integral, Differential) control system incorporating velocity feedback, velocity
MN1942 |