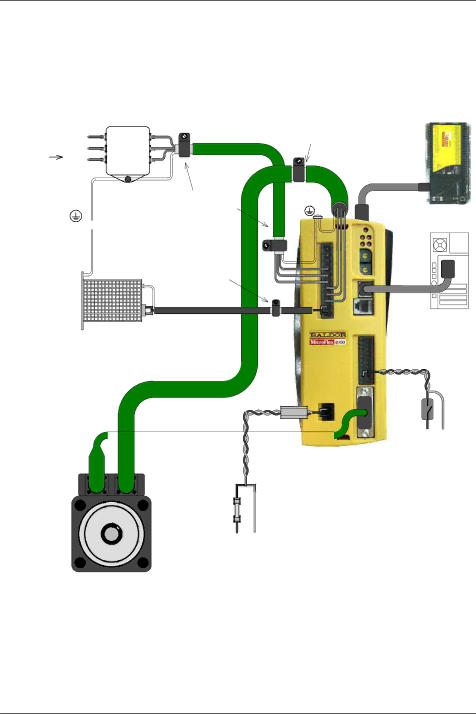
www.supportme.net
5.7 Connection summary - recommended system wiring
As an example, Figure 40 shows the recommended wiring necessary for the MicroFlex e100 to control a motor, while conforming to the EMC requirements for ‘industrial’ environments.
AC power
From | L1 | L1 | Filter | L1 | AC power in |
fuses | L2 | L2 | L2 |
| |
| L3 | L3 | L3 |
| |
|
|
|
Connect motor power cable shield to metal backplane using conductive shield clamp
Motion controller
PE
Star point
Optional regen resistor (Dynamic brake)
Connect AC power cable shield to metal backplane using conductive shield clamp (see section C.1.6).
Shielded twisted pair, clamped to metal backplane near drive using conductive shield earth/ground clamp (see sections 3.6 and C.1.6).
Regen
Motor power U V W
Ethernet
PC
USB
Ferrite
Motor feedback+24VDC 0V
Drive enable
input
2A |
Motor | +24VDC 0V |
|
Control circuit supply (fused). Use twisted pair cable with a ferrite sleeve (see section 3.4.8).
HThe MicroFlex e100 should be mounted on an earthed metal backplane.
HEnsure cables do not obstruct airflow to the heatsink.
HMotor represents a typical Baldor BSM motor. Linear motors may also be controlled by MicroFlex e100.
HConductive shield earth/ground clamps are not supplied.
HWhen using single phase supplies it may be necessary to reverse the AC power filter - see section 3.4.7.2.
Figure 40 - Recommended system wiring
MN1942 | Input / Output |